Abstract: The research on fire performance of new building materials is an important part of public protection and a necessary condition for its large-scale application in construction engineering. Although inexpensive calcium carbonate whiskers (CW) can improve the mechanical properties of cement-based composites at room temperature, the effect of high temperature on CW-reinforced cement-based composites has not been reported. In order to compensate for this deficiency, this study investigated the strength and microstructure changes of continuous cement paste and cement slurry after exposure to the evaluated temperature.
Key words: calcium carbonate whiskers; cement stone; high temperature
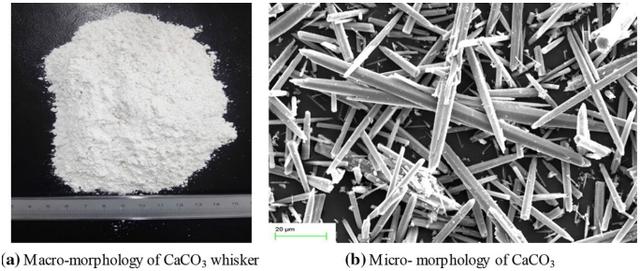
The macroscopic morphology (a) and microscopic morphology (b) of calcium carbonate whiskers were obtained by digital camera and scanning electron microscope, respectively.
Test Methods:
At 50 ° C to 100 ° C, some reactions of ettringite in the cement slurry begin to occur. Therefore, 60C is a suitable temperature for drying the sample without significant chemical reaction. The water loss rates of 0%, 10%, 20% and 30% continuous wave reinforced cement slurry after this preheating process were 3.2%, 5.4%, 7.0% and 8.7%, respectively. Caused. All prism samples were placed in an oven and heated at 60 ° C for 48 hours. The sample and continuous wave were heated from room temperature to a temperature of 200, 300, 400, 500, 600, 700, 800, 900 and 1000 ° C using a muffle furnace [37]. The target temperature is maintained for 2 hours. After heating the platform for 2 hours, the sample or continuous wave is still kept in the electric furnace, and gradually cooled to room temperature without opening the furnace door to avoid thermal shock [38]. Then, the mechanical properties of the samples exposed and not exposed to high temperatures were measured and compared. A total of 132 prismatic samples (3 samples per mixture) were tested for mechanical properties according to International Organization for Standardization 679. A three-point bending test was conducted with a support distance of 100 mm to obtain bending strength. The compressive strength is then determined by bending the two portions of the prism remaining after the test.
After the mechanical properties test, the sections were observed under a scanning electron microscope for microstructural analysis. At the same time, in order to evaluate the chemical bond between the whisker and the cement, the elemental composition of the continuous wave surface was also analyzed using a matched energy spectrometer. The thermogravimetric analyzer was carried out using a METTLER TOLEDO thermogravimetric analyzer/DSC1 in a dry nitrogen at a heating rate of 10 ° C / min in the range of 40 ° C to 100 ° C. The crystal phase of the coal water slurry exposed and not exposed to high temperatures was characterized using an x-ray powder diffractometer (XRD, Bruker D8 Advance, Germany) using CuKa12 radiation (k = 0.154 nm, 40 kV and 40 mA). Based on the microstructure and phase analysis, the enhancement mechanism of coal-water slurry to cement-based composites after high temperature is derived.
Results and analysis:
In general, the residual strength (including compressive strength, flexural strength, etc.) of cement paste and concrete decreases with increasing temperature. In particular, the change in residual strength of a cement-based composite after exposure to high temperatures can be divided into three phases:
1. In the stabilization and recovery phase, the strength of the cement-based composite material remains almost constant or even slightly increased from room temperature to about 40 °C.
2. In the fast loss phase, from 400 ° C to 800 ° C, the strength of the cement-based composite material is drastically reduced.
3. In the complete loss phase, almost all strength of the cementitious composite was lost after 800 °C.
This strength changes at high temperatures due to changes in the microstructure.
1. The decomposition of AFt/AFm occurs at approximately 115, which may result in a slight decrease in intensity. The strength recovery is caused by water evaporation and dry hardening from 150 ° C to 350 ° C. In addition, due to the "internal autoclave" effect, the evaporating water in the cement composite causes the hydrated cement particles and mineral admixture to continue to hydrate.
2. Dehydration of calcium hydroxide at 400 ° C to 600 ° C and destruction of carbon-hydrogen bonds results in a decrease in strength [ 22, 23 ].
3. Above 80 ° C, the decomposition of calcium carbonate and carbon sulfur hydroxide completely destroys the strength of the cement-based composite.
In addition, the pore structure change caused by the above chemical reaction is also an important cause of the change in strength.
3.2. Residual compressive strength
Figure 2 shows the residual compressive strength of the reinforced cement at different continuous wave concentrations after exposure to high temperatures. Table 3 summarizes the percentage increase in compressive strength of continuous wave or fiber reinforced cement compared to pure cement after exposure at different temperatures. The percent increase in residual compressive strength and residual compressive strength is shown as a function of temperature to assess the enhanced effect of continuous wave exposure to high temperatures. In terms of compressive strength, 10% continuous wave reinforced cement slurry usually achieves the highest compressive strength and the most effective strength, up to 600 ° C, as shown in Figure 2 and Table 3.
At room temperature shown in Table 3, the addition of 10% whiskers did not significantly increase the compressive strength of the cement slurry. As the content of coal water slurry increases to 20% and 30%, the compressive strength of cement paste decreases due to the increase of interface defects between coal water slurry and cement matrix, which is consistent with the results.
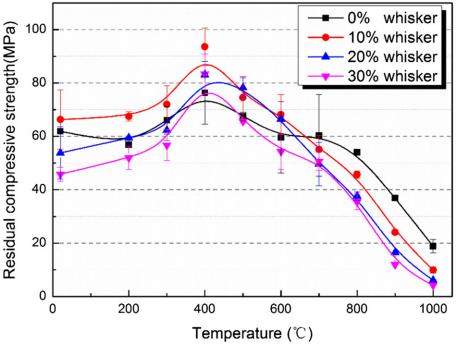
Figure 2. Residual compressive strength of whisker-reinforced cement slurry after exposure to the evaluated temperature. The result is an average of six samples. The standard deviation is also given.
The refractory research of new building materials is an important part of public protection and a necessary condition for its large-scale application in construction engineering. Calcium carbonate whiskers can improve the room temperature mechanical properties of cement-based composites. In addition, phase and microstructure changes of calcium carbonate at elevated temperatures are well known. Therefore, the effect of continuous wave on the mechanical properties of cement-based composites after high temperature is very different from that at room temperature. Therefore, in order to clarify the mechanical properties and microstructure changes of continuous wave reinforced cement-based composites at high temperatures, in order to withstand the continuous wave reinforced cement-based composites in practical applications, the study of continuous wave reinforced cement pastes in up to The strength and microstructure at an estimated temperature of 100 ° C were studied to compensate for this gap. Concluded as follow:
Continuous wave can improve the flexural strength and compressive strength of pure cement not only at room temperature, but also after exposure to an evaluation temperature of up to 60 ° C. In terms of compressive strength, 10% continuous wave reinforced cement slurry is generally below 600 ° C. Achieve the highest compressive strength and the most effective enhancement. For flexural strength, a 30% continuous wave reinforced cement paste typically achieves the highest compressive strength and the most effective reinforcement at 700 °C. The reason is that the compressive strength is more sensitive to the initial pores and cracks introduced by the CWs during mixing. The bending strength is more sensitive to the development of cracks, and CWs can inhibit the development of cracks during the fracture process. The flexural strength variability is greater than the compressive strength because the flexural strength is more sensitive to the microcracks during heating than the compressive strength. The flexural and compressive strength of the continuous wave after exposure to 600 °C of the cement paste is More effective enhancement.
The initial phase transition temperature from aragonite calcium carbonate to calcite is about 400 ° C, which can be demonstrated by XRD testing and scanning electron microscopy. During cement hydration and heating, continuous waves may bring different hydrated product phases: calcium (OH) 2 and carbon sulfur (i). Calcium carbonate produced by cement hydration is not as stable as continuous wave.
All coal water slurry exhibits better enhancement than low temperature in the temperature range of 40 ° C - 60 ° C. This is due to the phase change of Chinese stone calcium carbonate to calcite and the physical physics of autoclaving of cement slurry during heating. And the combination of chemical bonds. An increase in hydration of the whisker surface at 40 ° C demonstrates an improvement in physical and chemical bonds. In the temperature range of 80 ° C - 100 ° C, the decomposition of continuous wave makes the residual bending and compressive strength of continuous wave reinforced cement lower than that of pure cement.
On this basis, continuous wave can replace carbon fiber and polypropylene fiber as a refractory addition material for cement-based composite materials because it has a better reinforcing effect at an evaluation temperature of up to 60 °C. In addition, continuous wave reinforced cementitious composites have good mechanical properties and good economic benefits after exposure to an evaluation temperature of less than 600 ° C, and thus may be used as a protective material for fire-damaged structures.
Three Functions Hand Shower,Tri-Functional Hand Shower,Triple Function Handheld Shower,Square Push Dial Hand Showe
ASHOWER , https://www.ashower.com