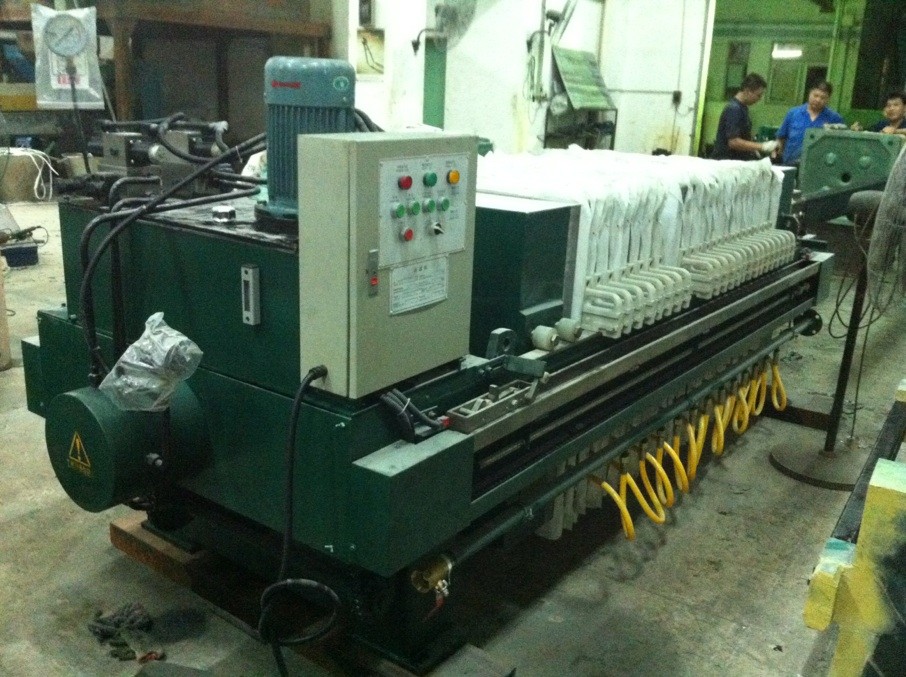
The diaphragm filter press has the advantages of high press pressure and good corrosion resistance. The new generation of diaphragms can be divided into materials: rubber diaphragm type and PP integral diaphragm type diaphragm filter machine working principle. The rubber diaphragm filter press is ideal for weak acid, weak base, and filter materials that are not organic solvents. The rubber diaphragm tympanic membrane is more adequate, and the pressure and gas volume used are relatively small, which can greatly reduce energy consumption. The PP separator is used in strong acid, alkali and organic solvent materials, and its performance is relatively more ideal and its service life is longer. Its pressing form is divided into gas (air, inert gas) press and liquid (water, oil) press to meet the needs of different industries. According to customer needs, the press component can be configured with food grade and common grade, and the control can adopt PLC and man-machine interface. For general materials, after 3-15 minutes of the diaphragm tympanic membrane, the effect of press dewatering can be fully exerted. For some special materials, the stepwise pressing method of high pressure pressing after low pressure pressing can also be used. The membrane filter plate can meet the filtration process of high-efficiency dehydration and can ensure the best filtration effect of the filter press. The working principle of the diaphragm filter can greatly reduce the moisture content of the filter cake and greatly increase the yield.
The diaphragm filter press works at the end of the feeding process, by pressing the filter cake to improve the dewatering efficiency of the whole machine, adding the dryness of the filter cake, reducing pollution and reducing labor. The drying process is eliminated in some processes. If the blowing operation is increased before and after pressing, the moisture content of the filter cake is further reduced.
The diaphragm filter press works with:
1, using low pressure filtration, high pressure pressing, can greatly shorten the entire filtration cycle.
2, using TPE elastomer, the maximum filtration pressure can reach 25MPA, so that the water content is greatly reduced, saving drying costs and increasing the yield.
3. Saving the consumption of operating power. In the late stage of filtration, the flow rate is small and the pressure is high.
4, diaphragm press function, complete this process in a very short time, saving power consumption.
5. Increase the degree of mud biscuits and reduce the content of mud cake. The diaphragm press presses the filter cake after the static filtration to make the structure of the filter cake rearrange, and the density is increased, thereby replacing a part of the water and improving the dryness. degree.
6, strong anti-corrosion ability, basically suitable for all solid-liquid separation operations.
7, configurable PLC and man-machine interface control.
8. The diaphragm filter plate has the characteristics of anti-fatigue, anti-aging and good sealing performance.
The working principle of Zhangzhou Donglong Diaphragm Filter Press can improve the processing capacity of the filter press and increase the operational flexibility of the filter press, especially the operation of mud cake cleaning.
Diaphragm filter press working principle:
1. Positive pressure and strong pressure dewatering, also known as slurry dewatering, that is, a certain number of filter plates are closely arranged in a row under the action of strong mechanical force, and a filter chamber is formed between the filter plate surface and the filter plate surface, and the filter material is strong. The positive pressure is sent to the filter chamber, and the solid portion of the filter material entering the filter chamber is trapped by a filter medium (such as a filter cloth) to form a filter cake, and the liquid portion is filtered through the filter medium to discharge the filter chamber, thereby achieving the purpose of solid-liquid separation. With the increase of positive pressure, solid-liquid separation is more thorough, but from the perspective of energy and cost, too high positive pressure is not cost-effective.
2. A filter press equipped with a rubber extrusion film, the compressed medium (such as gas, water) enters the back of the extruded film and pushes the extruded film to further dehydrate the squeezed filter cake, called extrusion dewatering.
3. The compressed air enters the filter cake on one side of the filter cake, and the liquid water is carried from the other side of the filter cake through the filter cloth to discharge the filter chamber for dehydration. If the filter cloth is applied to both sides of the filter chamber, the liquid portion can pass through the filter cloth on both sides of the filter chamber and exit the filter chamber to dewater the filter chamber.
4. After the dewatering is completed, the mechanical pressing force of the filter plate is released, and the filter plate is gradually opened by a single block, and the filter chamber is opened separately to perform the unloading of the cake as a main working cycle.
According to the nature of the filter material, the working principle of the diaphragm filter can be set separately for slurry dewatering, extrusion dewatering, wind blowing dehydration or single and double side dewatering, in order to minimize the filter cake moisture.
Website contact Mr. Wu 13760177211 Email @163.com
fax
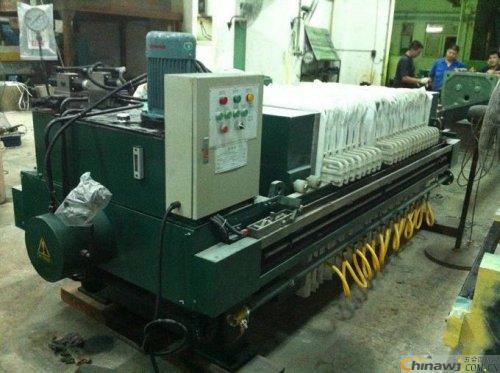
Flame Retardant Fabric,Fire Resistant Fabric,Cotton Fr Fabric,Fire Protective Fabric
Xinxiang Worldbest Patron Saint Co., Ltd , http://www.xxhyhsworkwear.com