The 6700 knuckle is mainly used for 6-7m long passenger car chassis and some series of light trucks. With the increase of the company's passenger car chassis and light truck production, the 6700 knuckle demand is getting larger and larger, and the 6700 knuckle φ38mm step hole In the process of processing, due to the defects of the fixture and the tool, the product quality is unstable, the processing efficiency is low, and the production demand cannot be met, which becomes the bottleneck process of the 6700 knuckle production line. In order to improve the production capacity and meet the technical requirements of product quality, a reasonable improvement plan was drawn up through in-depth study of fixtures and tool structures.
Original fixture status
The original fixture adopts the way of guiding and supporting the guide rod. The knuckle is positioned by the outer circle of the upper and lower positioning sleeves of the clamp during machining; the outer circle size of the upper and lower positioning sleeves is smaller than the minimum value of the knuckle main pin hole size φ34+0.03 +0mm by 0.03mm, so the clamp positioning sleeve is outside. The gap between the circle and the inner hole of the workpiece is loose. At the same time, the gap between the tool guide pin and the inner hole of the clamp positioning sleeve also forms the same type of looseness, and the guide pin is too thin and the overhang is long, resulting in poor guiding rigidity. Moreover, the workpiece has no clamping device, and the workpiece and the tool are mutually oscillated during machining, so that the finished product has irregular hole shape, hole position deviation and chipping of the hard alloy overall boring blade.
Original tool status
In addition to the accumulated clearance of the original fixture, the original tool uses a welded ordinary hard alloy overall boring tool. This positioning method mainly relies on the guide pin on the tool. During the machining, there is a gap between the outer circumference of the tool guide pin and the inner hole of the clamp positioning sleeve. The formation of loose rafts, as well as the lack of guiding rigidity caused by the limited diameter of the guide pin on the tool. For this kind of welded ordinary hard alloy integral boring tool, there are also some shortcomings: First, the soft blade is easy to wear, and the pre-wearing of the main cutting zone at the front of the tool makes the hole shape quickly and straight, and the ordinary oxygen welding When the flame masters the uncertainty and the cold-free forced dry grinding, the potential damage of the tool manufacturing process, the four-blade radial component asymmetry caused by the partial damage makes the shape size out of control; second, the cutter is forced to lose sharpness due to wear and tear. Cutting, the hole wall roughness is deteriorated, the blade force is suddenly increased, the single-blade or multi-blade cracking, and the instantaneous scrapping often occurs, and the tool manufacturing cycle is long, the repair and manufacturing supply is sluggish, and the phenomenon of off-supply often occurs, causing the production line to stop. The line waits for the tool.
Current fixture status
The fixture (see Figure 1) follows the principle of uniform positioning. The design uses one side and two pin positioning methods. The workpiece is machined by the flanged surface and the flanged surface of the flange. The positioning is accurate and reasonable. After the workpiece is in place, the cam clamp is used. The pressing plate is quickly pressed, changing the phenomenon of no clamping device. Through the improvement of the fixture, the positioning of the upper and lower positioning sleeves of the original fixture by the fixture is eliminated, and the outer circle size of the positioning sleeve is smaller than the minimum value of the knuckle main pin hole size φ34+0.03 +0mm by 0.03 mm. The gap between the clamp positioning sleeve and the inner hole of the workpiece swings with each other, and the positioning accuracy is poor, thereby improving the clamping efficiency and the product quality.
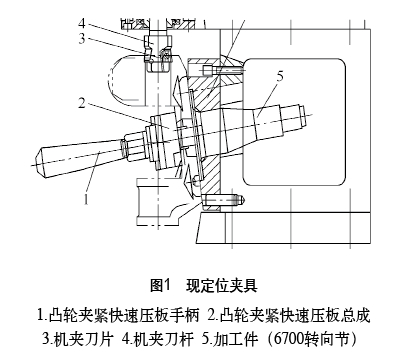
Current tool status
In order to improve the performance of the tool and the quality of the cutting, some improvements have been made to the tool. Firstly, the original welded ordinary hard alloy boring tool is changed to the self-made machine knives; secondly, the bearing set is added to the arbor (the bearing set plays a fixed supporting role, and at the same time, the bearing set also increases the rigidity and rotation of the arbor The role of precision) ensures that the tool holder is concentric with the clamp bearing set during machining without offset.
In order to ensure that the machine clamp tool achieves the above effects, the tool bar portion is machined on the T617 trampoline. The improved tool is shown in Figure 2. The machining process is carried out by using the functions of the bench vise, the auxiliary positioning block and the rotary disk, and the processing of the longitudinal and horizontal distribution and the symmetric distribution and the angular distribution of the two-boring blade groove and the chamfering blade groove are completed, and the specific processing of the clamp is also adopted. The clamping work is completed once on the trampoline, thus ensuring good positional accuracy of the pins, faces and holes.
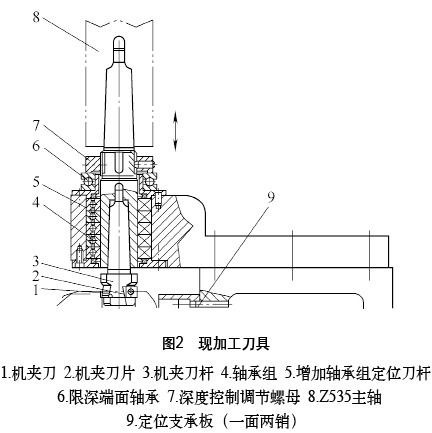
The improved knives have the following advantages: only one machine clamping arbor is required; the multi-blade locating blade has high utilization rate; the blade is a universal model, the supply is sufficient, and the cost performance is high; the blade has the same shape, chip groove, edge angle and precision. Sex, high processing accuracy.
Get results
Through the improvement of the above two aspects, a good effect is achieved.
(1) Chip removal condition When the original fixture is processed, the slag-like debris is easy to stick to the outer circle of the upper positioning sleeve, so that the positioning is deviated, and it will also fall between the guide pin and the inner hole of the positioning sleeve, causing the two to bite when rotating. Knot. Now the lower part of the cutting area of ​​the fixture is a complete cavity, which has good chip evacuation conditions and does not cause positional deviation.
(2) Function setting processing mode is changed from boring to boring to achieve high-efficiency cutting. The new fixture makes the shape and position accuracy fundamentally improved; the original processing method is divided into two steps, first processing φ38mm hole, then chamfering, when processing The pupil is chamfered with the chamfering, which saves processing time and ensures the positional accuracy due to the same pin-and-pin positioning method as the other processes. The clamping plate cam mechanism on the clamp enables fast and reliable clamping. An end bearing is mounted above the clamp to make the depth of cut control reliable.
(3) The high rigidity of the system rigid fixture structure, the high rotation precision of the bearing set, and the extremely short mast overhang constitute a high-quality boring condition, which enables the processing of the vertical drilling machine to achieve the processing effect of the special boring equipment. .
(4) Quality effect Because the workpiece is positioned reasonably, and the clamping plate is pressed and the positioning pin is positioned, the workpiece is safe and stable during processing, and the tool is improved, the bearing assembly is properly installed, the chip removal performance is good, and the overall rigidity of the fixture is excellent. To ensure product accuracy.
(5) Output effect Since the function setting is reasonable, high-speed and high-efficiency cutting is realized, and the auxiliary time of the processing process is reduced, and the process is basically in a maintenance-free state, so that the production efficiency is multiplied.
Conclusion
Through the improvement of the 6700 knuckle φ38mm step hole machining process, clamping fixture and tool, the gap between the fixture and the workpiece positioning device and the positioning accuracy caused by the mutual movement of the workpiece and the fixture are eliminated, thereby improving the positioning accuracy and loading. Clip efficiency. Moreover, it eliminates the wear and tear of the welding tool blade, the uncertainty of the flame control during oxygen welding, the sudden forced dry grinding of the cold and the sudden force increase of the blade, the single-blank or multi-blade cracking, and the long production cycle, thereby improving the cutting of the cutter. Accuracy and cost of use. At the same time, the machining efficiency and processing quality of the 6700 knuckle φ38mm stepped hole are improved.
Rx Ring Joint Gasket,Rx Ring Gasket,Rx And Bx Ring Gasket,Rx Ring Joint Gaskets
WENZHOU JINGWEI SEAL TECHNOLOGY CO., LTD , https://www.ringjoint-gasket.com