Abstract 1 Evaluation of the testing machine 1.1 Characteristics of the testing machine 1.2 The test operation process partially perfected the testing machine
2 Uncertainty test on test machine 2.1 Description of uncertainty 2.2 Method used in this test 2.3 Test results 2.4 Analysis of test results
3 Study on the influence of grinding test condition parameters on test results 3.1 The effect of different grinding pressure on the grinding performance of the belt 3.2 The effect of different working speed on the grinding performance of the belt 3.3 Different belt speeds on the belt belt Effect of cutting performance 3.4 Effect of different test piece speed on the grinding performance of the belt 3.5 Effect of cooling measures on the grinding performance of the belt
4 DISCUSSION 4.1 Discussion on the test mode of constant feed grinding 4.2 Discussion on the test piece of round pipe 4.3 Preliminary recommendations for the development of a new procedure for the detection of abrasive belt grinding performance 4.4 Discussion of other issues related to the development of the procedure 4.5 Improvement of the test machine Suggestion conclusion
Presented by the Expert Committee of the Applied Abrasives Branch, the member of the expert committee of the branch, Professor Li Daoyu, the creative concept of the senior engineer and the SDSY-50B CNC belt grinding performance testing machine designed and manufactured by Suzhou Sufuma Machinery Co., Ltd., since November 2013 After being exhibited at the second Sanmei Exhibition in Zhengzhou, it was successfully installed in the internship workshop of Henan University of Technology, and officially started the test in February 2014. The purpose and tasks of the test drive are:
1) Through the test run, evaluate whether the test machine meets the requirements of the belt grinding performance test; find and solve the problems existing in the design and manufacture of the test machine;
2) Perform the uncertainty test of the test machine;
3) Accumulating experience and data for the development of new procedures for belt grinding performance testing methods through tentative testing of abrasive belt grinding performance.
According to the above three tasks, the three-month test practice and experience are introduced as follows:
1 Evaluation of the testing machine
1.1 Characteristics of the test machine
In the past three months, we have carried out more than a thousand grinding tests and experienced many of the characteristics of this testing machine. The conclusions are as follows:
1.1.1 The control of the test machine is very convenient
SDSY-50B CNC belt grinding performance testing machine is to realize the exchange of data and information between man and machine through the upper computer (Figure 1-1, 1-2, 1-3 and 1-4), grinding each Kinds of working conditions, such as: belt line speed, grinding pressure, belt tension, specimen rotation speed, radial feed rate, grinding time can be pre-set using the keyboard, according to our hands-on practice Experience, as long as someone who has used the computer experience can quickly master the operation of the test machine. After all the test conditions have been set, the subsequent test process will be automatically performed according to the predetermined procedure.
When the test machine is working, the test piece will advance to a distance of 10mm from the abrasive belt at a certain speed from the starting point, and then turn to slow feed, to 0.5-2mm from the abrasive belt (specifically selectable), and then automatically reduce to The working feed speed is contacted with the abrasive belt; when the grinding really occurs, the grinding timing is automatically started. When the predetermined grinding time is reached, the feed is automatically stopped. At this time, the test piece does not immediately retreat, but again Grinding for a certain period of time until the predetermined no-feed grinding time is completed, then quickly returning to the starting point, thereby completing a grinding work cycle. After that, pause for a certain period of time, that is, after the set interval time, start the next grinding work cycle. Since all of the above actions are controlled by a computer-set program, there are few places where the operator needs to intervene artificially, and it is convenient to manually tension the belt and adjust the tension.
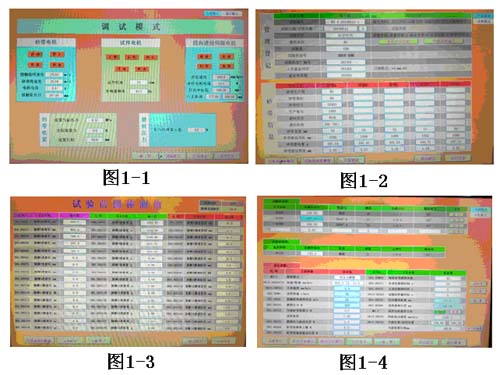
1.1.2 The applicability of the test machine is very extensive
The test machine can grind two types of test pieces: round bar and round pipe; there are two methods of constant pressure grinding and constant feed grinding in the test mode; the equipment is shipped with three kinds of diameter contact wheels. It can be replaced as needed; the adjustment range of the belt line speed is 5-40m/s, and the adjustment range of the grinding pressure is 50-500N; the above aspects are optional and can fully adapt to various types of belt grinding performance. The need for testing fully demonstrates the wide applicability of the testing machine.
From the experience of our test run, the test cost of the round test piece is low and convenient, but in the case of the current market supply is not very standard, it is really difficult to ensure the consistency of the material; the round test piece The grinding state is close to the actual production process, especially in the grinding zone, the heat dissipation condition is good, and the grinding temperature rise is small, which is very beneficial to the testing of the abrasive belt grinding performance. In addition, the quality of the round pipe is much larger than that of the round bar, which can reduce the test time. The number of times the test piece is reloaded is advantageous for ensuring the stability of the grinding test.
The constant pressure grinding test mode is a relatively customary method in the coated abrasive industry, and it is close to the manual grinding state in actual production. The constant feed grinding test mode has control from the performance of this test run. It is convenient, the process is stable, the test uncertainty is small, and the model is more suitable for the occasion where the mechanical belt grinding on the production line has requirements for the beat. It should be a test mode worthy of attention and popularization.
1.1.3 The test process can automatically collect and record various working parameters.
Belt grinding speed, belt motor current, belt slip ratio, grinding pressure, belt tension, belt elongation, specimen rotation speed, radial feed rate, servo motor active during grinding test The instantaneous values ​​and trend graphs of the 11 working parameters such as current, grinding time and length of specimen cut-off can be automatically collected and displayed on the display in real time (Figure 1-5).
In addition to using the data method to monitor the dynamics of the test process in real time, the test machine also uses the trend graph to show the changes of the parameters. The trend chart is divided into three types: A, B, and C:
The Class A trend chart (Figure 1-6) reflects the variation of the four parameters of the belt line speed, the belt grinding motor current, the grinding pressure and the belt slip rate with the grinding time.
The B-type trend graph (Figure 1-7) reflects the variation of the belt tension, the belt elongation, and the specimen speed with the grinding time.
The C-type trend graph (Figure 1-8) reflects the variation of the three parameters of the feed rate of the test machine, the active current of the servo motor, and the radial feed coordinate with the grinding time.
The chart can be saved for one month, making it easy to analyze and find after the test. It is also possible to read the average, maximum, minimum and standard deviation of each parameter for a given time period on the trend graph.
These features are very convenient for the tester to understand and analyze the progress of the grinding process.
The machine also has a variety of fault alarm and fault history file records (Figure 1-9), each fault has a record to check, easy to repair and maintain the equipment, but also easy to analyze the cause of the fault; Conducive to the safety of people and equipment.
After the grinding test is completed, the test machine will automatically generate a “sand belt grinding performance test record†and a “sand belt grinding performance test report†(or “sand belt grinding performance comparison reportâ€) and other forms for printing. The degree of human intervention during the whole test process is significantly reduced; this not only reduces the work intensity of the tester, but also plays an important role in preventing human error and ensuring the accuracy of the test.
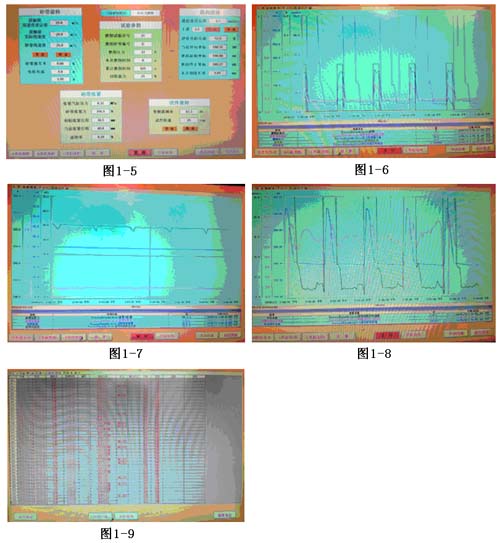
1.1.4 The test machine is finely manufactured, runs smoothly, and the test results are credible.
During the running process, it can be felt that the contact wheel runs very smoothly at high speed and the vibration is small; the feeding system composed of servo motor, ball screw and linear guide has high positioning accuracy and good repeatability; indication error of each parameter In accordance with the predetermined requirements, especially the speed of the belt line can be kept constant during the test, and the error with the set value can be completely controlled within 1%.
Tests on the uncertainty of the test results show that the data from the abrasive belt grinding test is credible and will be described later.
The testing machine can also automatically measure the length of the resection of the test piece, thereby using the volume calculation to determine the weight of the metal to be removed by the grinding, and eliminating the need for the test machine to be weighed once the previous test machine has to be ground once; It is only necessary to measure the pre-grinding weight of the test piece and the weight of the test piece after the grinding of the abrasive tape sample, which not only improves the working efficiency but also reduces the working strength of the tester. The results of several tests confirmed that the error of this method compared with the weighing method is about 2%, which is completely within the acceptable range, which also reflects the fineness of the overall manufacturing of the testing machine.
1.2 The trial operation process partially perfected the test machine
Because it is the first prototype of the trial system, some problems in the design are inevitable and normal. One purpose of the test is to find the problem and improve it. Through the trial run, the following three main problems have been discovered and improved, which are introduced below.
1.2.1 solved the problem of early timing
“Advance timing†means that the grinding timing has started when the grinding has not actually started, so that the grinding correction amount has excessive error data, which affects the accuracy of the test result. During the 475 grinding process during the period 2.21-3.14, a total of 30 pre-times occurred, with an occurrence rate of 6.3%.
Cause Analysis:
1. There is interference in the external power supply;
2, the benchmark sampling point program has a problem of poor design.
Perfect situation: The program has been perfected, and the sampling time of the timing reference point is shifted from the “fast-to-slow†phase to the “slow-transfer†phase, and the timing conditions are appropriately modified; after March 27, the running state is normal, no Similar problems are repeated.
1.2.2 Improve the protection program when the belt is broken
A belt breakage failure occurred on March 28, and the original design protection procedure did not work, resulting in a crash and the contact wheel rubber layer was destroyed. After reviewing the trend graph at the time of the failure (Figure 1-10), it was found that the conditions for setting the protection program were unreasonable. The condition of the initial breakage protection is that the protective action is initiated when the elongation of the abrasive belt is greater than 5%. In fact, the elongation of the abrasive belt is reflected by the extension of the tensioning cylinder, and the movement of the cylinder is slow, and the protection cannot be quickly started. action. The fastest information reflected in the belt breakage is the sudden change of the belt line speed. Therefore, the program is perfected as a signal. After the artificial strip test, the protection action is confirmed to be normal; no similar problems have appeared in the future.
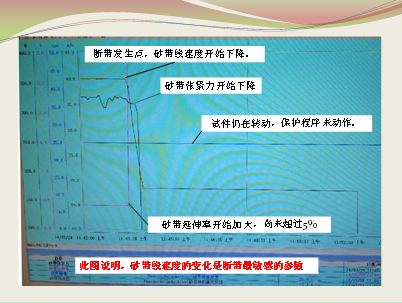
1.2.3 Further improve the contents of the test report and record sheet
In the test run, there are some unsuitable problems in the grinding belt performance test report and the belt grinding performance test record table; for example, the calculation unit should be “minâ€, but the program is in “sâ€; There is an error in the calculation formula of the test data; the effective digits of some data need to be adjusted; the correlation between the record table and the test report is not reflected; the data recording needs to shorten the grinding time and increase the number of grinding times cannot be adapted; a column needs to be added directly “Grinding capacity†data reflecting the degree of change in the grinding performance of the belt.
The relevant procedures have been rewritten as required, and all calculation formulas and data units have been corrected. The trials after March 27 have been published in the new format, which is more in line with the user's requirements for test results. . It also adds a variety of forms for grinding times of 50, 75, 100, etc., which are available for selection.
Table 1-1 and Table 1-2 show the samples of the Abrasive Belt Grinding Performance Test Report and the Abrasive Belt Grinding Performance Test Record of the Association's public technology service platform:
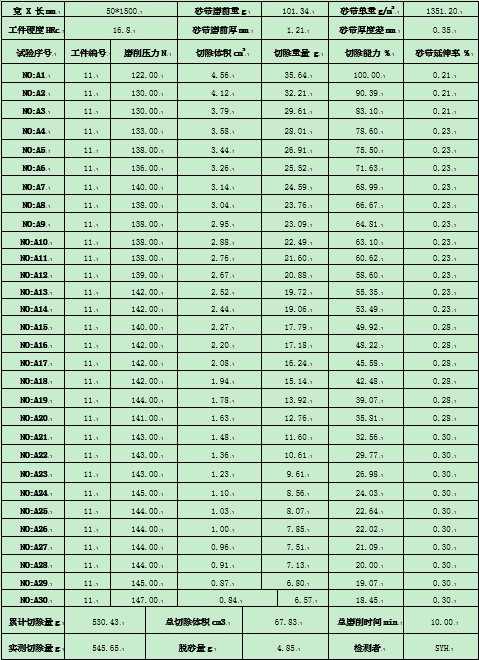
China Machine Tool Industry Association Coating Abrasives Branch Public Technical Service Center Belt Grinding Performance Test Report
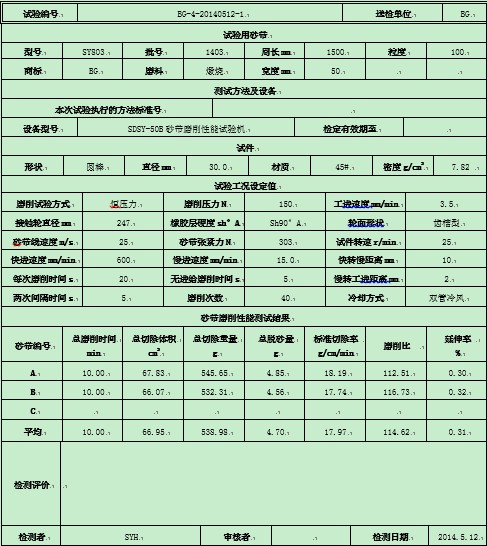
1.2.4 Added the identification of the grinding time zone on the trend graph
The original trend graph does not reflect the start time of the grinding and the end time of the feed grinding. It is not convenient to monitor and analyze the process during the test. The identification of the grinding time section has now been added to the trend graph (Figure 1-11).
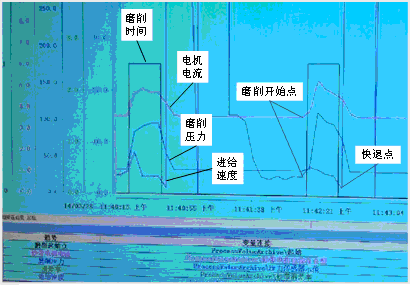
POLYKEN 934 is a Cold Applied Tape coating system designed for the corrosion protection of field joints, fittings, and specialty piping. The highly conformable backing and thick, aggressive adhesive also make it the ideal repair system for all types of main line coatings. The POLYKEN 934 tape with very tacky adhesive has a release plastic liner to enable proper unwinding of the roll. Whether used as a double wrap system or as a single wrap with a mechanical layer, the POLYKEN 934 tape coating system is universally specified in the oil, gas and water industries.
Polyken 934 Anticorrosion Tape
Polyken 934 Anticorrosion Tape,Corrosion Protection Tape,Anticorrosion Polyethylene Tape,Anti Corrosion Adhesive Tape
Jining Qiangke Pipe Anticorrosion Materials CO.,Ltd , https://www.pipe-wrap-tape.com