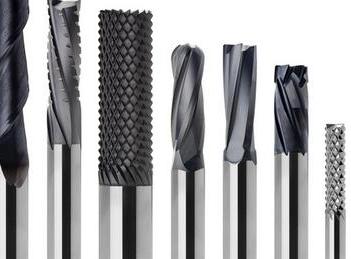
Superhard material tools have the characteristics of high processing efficiency, long service life and good processing quality. In the past, they were mainly used for finishing. In recent years, due to the improvement of the production process of man-made superhard tool materials, the purity of raw materials and the grain size have been controlled. With the use of composite materials and hot pressing technology, the scope of application has been continuously expanding. In addition to being suitable for general finishing and semi-finishing, it can also be used for rough machining. It is internationally recognized as the most promising tool material for improving productivity in the modern era. one. Using superhard materials to process steel, cast iron, non-ferrous metals, and alloys, etc., the cutting speed can be an order of magnitude higher than that of cemented carbides, and tool life can be tens or even hundreds of times higher than that of cemented carbides. At the same time, its appearance has also changed the traditional concept of the process. The use of super-hard tools can often be directly used to car, mill grinding (or polishing), hardened parts processing, single process can replace multiple processes, greatly reducing the process flow .
Diamond material cutters have extremely high hardness and wear resistance, and can effectively process non-ferrous metals such as copper and aluminum and their alloys, ceramics, unsintered hard alloys, various fiber-reinforced composite materials, and the like. Diamond commonly known as "Diamond drill", which is what we often say diamonds. Natural diamond deposits have been formed before history and no growth rules can be followed. “Synthetic diamond is mainly used in the military industry and aerospace industry. Because of its high temperature, high pressure, the helmet film of astronauts, the insulation board of aviation spacecraft, and the sleeper of high-speed rails, etc.†Henan Research Institute of Diamond and Product Engineering Professor Wang Qinsheng, the chief engineer of the center and the host of the project, introduced that synthetic diamond is also widely used in advanced manufacturing and modern processing industries, from dental dental prosthetic teething knives, cosmetic knives, to automotive bearings and electronic components. Use it to get it. The large-sized corrugated sheets inlaid with synthetic diamonds can be used to cut huge stones and highway cement, and have also played an important role in geological exploration and oil exploitation.
Introduction to the diamond industry chain: The diamond industry chain is graphite, single crystal, micro powder, polycrystalline composite sheet and diamond products from top to bottom. At present, about 50% of single crystals in China are used to produce sawing tools. According to the different application fields of polycrystalline products, polycrystalline composite sheets are divided into: oil-opening, mining-opening, tool-use, drawing-die blanks. Diamond products are divided into monocrystalline products (abrasive tools, sawing tools), polycrystalline products (geological drills, cutters, drawing die). Introduction to downstream applications: Abrasives are mainly used in IC chip processing in the electronic information field, engine processing in the automotive field, air conditioning and refrigerator compressor processing, tool processing, etc.; sawing tools are mainly used in stone industry, construction industry; drilling tools are mainly used In mining, oil extraction; cutter is mainly used in lathe processing. Market space forecast: In 2011, the domestic single crystal market demand will be approximately 9.4 billion carats. The growth rate will be 11.33% and 10.33% in the next two years. In 2011, the demand for global oil composite sheet will reach 7.8 billion yuan, and the growth rate will be 12% in the next two years. 92 billion yuan, the growth rate of 12% in the next two years; cutter composite film 13.2 billion yuan, the growth rate of 45.33% in the next two years.
Cubic boron nitride, like polycrystalline diamond, is also synthesized at high temperatures and pressures. Its polycrystalline structure and properties are similar to that of diamond. It has high hardness, good thermal conductivity, small thermal expansion, and small Density, lower fracture toughness. In addition, cubic boron nitride also has excellent chemical and thermal stability, and it hardly reacts with iron group elements, which is superior to diamond. Compared with diamond, cubic boron nitride has higher thermal stability, chemical inertness to iron group elements, strong anti-bonding ability, and is more suitable for processing various hardened steels, thermal spray materials, chilled cast irons and HRC35 and above. Cobalt-based and nickel-based hard-to-cut materials.
In industrialized countries, cubic boron nitride tools have been widely used in automotive, heavy machinery and other machining industries. The cubic boron nitride tool is suitable for high-speed dry cutting and can process high-speed gray cast iron at a speed of over 2000 m/min. Cubic boron nitride tools are also widely used in high-speed hard cutting applications, especially in the machining of alloy steel parts on automotive engines, such as gears, shafts and bearings between HRC 60 and 65. These parts used to be based on grinding. To ensure dimensional accuracy and surface quality. "As we all know, the main component of cemented carbide inserts is tungsten carbide, which is a scarce resource. Although China is a country rich in tungsten, according to the current level of development and use, tungsten carbide resources will be rapidly reduced. Some experts predict that The next 60 years may dry up, and new superhard cutting tools will play a greater role in the future of cutting.
It can be used for both finish machining and semi-finishing, as well as for rough machining with up to 6mm. At present, the annual consumption of cubic boron nitride in the world is about 10% to 15%. Artificial cubic boron nitride superhard tool material, the current single crystal to coarse grain, high strength, multi-directional development. The single crystal CBN produced by Japanese inorganic materials has a diameter of 3mm. PCBN products manufactured by De Beers Company have a maximum diameter of 101.6mm, and are then laser-cut to any desired shape to process 70HRC high-hardness materials.
Overview of Development of Superhard Material Tool Industry Today, the advantages of superhard material cutting tools in cutting machining are well known by the masses of users and have been more and more widely recognized and applied. The market demand is huge.
Judging from the superhard material itself, China has obvious resource advantages. It has recently been discovered that most of the diamond exploration drill holes in the Wafangdian area were only 200-300 meters. The overall shape of Kimberlite cannot be effectively controlled. Nearly 1,000 meters in the hole, more than 800 meters in the thick Kimberley to see the body, can explore millions of carats of diamond resources.
At present, China's diamond production accounts for more than 80% of the world's total production, and cubic boron nitride (CBN) production accounts for more than 60% of the world's total production. It is already the world's largest producer of super-hard materials, and China has taken the lead in superhard materials. In the ranks of the world’s most powerful countries, China’s superhard material industry has taken the lead in becoming one of the internationally speaking industries.
The composite superhard cutting tool market is currently dominated by foreign manufacturers. In 2009, the top companies in the global market share of composite superhard cutting tool materials were all foreign companies, namely Element Six (30%) and DI Company ( 20%), Japan's Sumitomo (18%), South Korea's Nikko (9%), MegaDiamond (4.5%), TomeiDiamond (4.5%), Dennistools (4%), and several major companies accounted for 90% of the market.
In the market of non-composite superhard cutting tools, cubic boron nitride monolithic polycrystalline inserts are already a strong point in China. FuNiKe is not only useful in advanced polycrystalline cubic boron nitride (PCBN) blades technology, but also in cubic nitrogen. The boron-bonded super-bonded blade has advanced technology and is unique in China's superhard cutting tool industry. It has advantages in welding the integrated benefits of polycrystalline boron nitride inserts.
The square nut is one of the welding nuts. The welding method is believed to be known to all. It is to use high temperature to melt some metal and weld it between the two products to play a fastening role. The fastening effect of this connection will be very good and will not be easy to loosen. It can also be used with bolts. Square nuts are mainly used in electric power engineering, road traffic, home building materials and other industries.
Square Nut,Square Nut Bolt,Square Weld Nut,Square Nuts And Bolts
Jiangsu Jiajie Special Screw Co., Ltd , https://www.jiajiescrewcompany.com